In order to improve the parts distribution process, the Volkswagen Volkswagen launched a project, part of which is to replace the cardboard boxes of the current factory transport parts with RFID tags and reusable plastic containers. This application allows the Puebla plant to reduce the cost of parts distribution per year by 30% by reducing packaging costs and automated cargo confirmation processes, according to Juan Manuel RodrÃguez Flores, sales manager at system integrator GrupoHasar.
In the second half of 2007, the Mexican public hired GrupoHasar to design a program to help the company reduce the manual steps required to send parts to dealers. After the pilot test, the company officially launched the system in July 2008. Now, Volkswagen and GrupoHasar have jointly extended the system to other Volkswagen plants in Mexico.
The Puebla plant in Mexico uses a labelled, reusable plastic container.
When the dealer submits a retail order to the Puebla factory, the SAP Enterprise Platform Planning Software used by VW captures this information and forwards it to the Factory Warehouse Management System (WMS). After receiving the order, the factory employee drives the forklift truck to the warehouse to collect all the required parts. They use a handheld scanner to read the bar code for each part and then place the part on a packaging table. Currently, Flores claims that because RFID tags are too expensive to replace bar codes on a single item; if tag costs fall in the future, the Puebla plant may switch to RFID tags, further individual parts.
At the packaging table, another employee uses a handheld barcode scanner to read the bar labels of reusable containers. The tag is embedded with an RFID tag - AlienTechnologySquiggle Passive UHFEPCGen2 tag. Barcodes and tags are coded with the same ID code. The ID code is collected using a handheld scanner and the worker scans the bar code of each container part. When he is done, the handset associates the retail ID code with the container ID code and then uploads the data to the WMS.
In the warehouse management software, the order status is updated to indicate that the order has been packaged. A Motorola XR440 RFID reader installed at the loading station captures the ID number of the RFID tag before the container is loaded into a truck and ready for shipment to the dealer. This information is also forwarded to the WMS, identifying the completion and delivery of the order, with the date, time, and delivery warehouse. When the dealer receives the parts, the bar code label on the container is read one by one and registered in the WEB-based WMS, so that the Puebla factory knows the receiving time of the container.
Currently, only 30% of the mass dealers who order parts from Puebla receive plastic containers with RFID tags. These dealers receive parts from the Puebla plant twice a week, and the container return process is very simple: the dealer returns the empty container when it receives the new container.
When empty containers are returned to the Puebla warehouse, they pass through a channel RFID reader and are then returned to the factory's container inventory. If the record shows that the dealer failed to return to the labeling container within 10 days after receiving the goods, he will be fined.
Currently, the factory has adopted 16,000 RFID tagged, reusable containers. In addition, the factory has 350 labeling metal carts. The cart label is the Intermec Passive EPCGen2 label, which protects the housing from cushioning the metal appearance of the label and cart.
Reusable RFID containers not only save the ever-increasing cost of cardboard containers at the Puebla plant, but Flores says it also greatly reduces packaging waste.
Taking into account the advantages of the new tracking system - reducing packaging costs, faster shipping confirmation system - Mexico Volkswagen hopes to replicate the system at the parts distribution factory in Guadalajara and Monterrey. In the second half of this year, Flores said that Volkswagen's US parts distributors may also use this RFID system to track parts shipments.
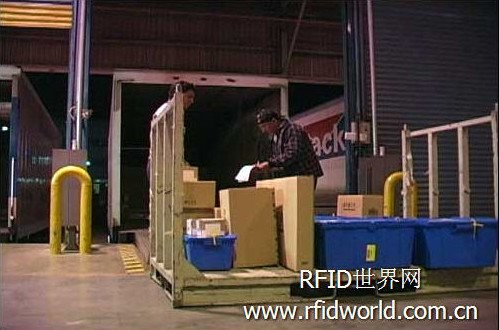
Product categories of Nutrition Porridge Machine, This production line produces convenient and delicious nutritious porridge.
We are specialized manufacturers with 15 years of extruder experience, we have the perfect after-sales service and technical support. We can provide customers with personalized Nutrition Porridge Machine equipment or complete plant layout and production lines to meet customer needs.Look forward to your cooperation!
Nutrition Porridge Machine, Automatic Nutrition Porridge Production Line, Instant Porridge Making Machine, Instant Porridge Making Machine
Jinan Chenyang Technology Co., Ltd. , https://www.cyricestrawproductionline.com