I. Introduction
What is a press brake used for? In the sheet metal fabrication industry, the bending machine is regarded as an indispensable tool for standing out and is specially designed for bending arts. The press brake operates by clamping the workpiece between a matching punch and die, applying force to create a predetermined bend.
In essence, a press brake is a machine that bends sheet metal and plate metal with precision and transforms the flat workpiece into a precise shape and structure. This forming ability is mainly attributed to metal ductility. Ductility refers to a sort of ability that metal is stretched and bent without breaking, which emphasizes the reason why metal is popular among various industries.
From the sleek curves of the car's chassis to the intricate design of the metal arts, the need for metal forming and fabricating is paramount. First of all, let's watch the video first:
II. Different Types of Press Brake Uses
There are several types of press brakes, and each piece has its specific uses:
Mechanical Press Brakes
Mechanical press brakes are among the earliest types of press brakes, known for their simplicity and reliability. They operate using a flywheel that stores energy and releases it to perform the bending operation. These machines are typically used in applications where high-speed production is required, such as in the automotive and appliance industries.
Mechanical press brakes are favored for their ability to deliver consistent performance and are often employed in environments where the demand for rapid, repetitive bending is high. However, they may lack the precision and flexibility offered by more modern press brake technologies.
Hydraulic Press Brakes
Hydraulic press brakes have become a staple in the metalworking industry due to their versatility and power. The machine tool drives the ram movement with two synchronized hydraulic cylinders on the C-frames. These hydraulic machines utilize hydraulic cylinders to exert bending force, allowing for greater control over the bending process.
Tonnage refers to the bending force of the particular press brake. This type of press brake is ideal for handling thicker materials and producing complex bends with high precision.
Industries such as aerospace and heavy machinery manufacturing often rely on hydraulic press brakes for their ability to deliver consistent results across a variety of materials and thicknesses. Additionally, hydraulic systems provide smoother operation and can be easily adjusted for different bending requirements, making them a popular choice for custom fabrication projects.
CNC Press Brakes
CNC (Computer Numerical Control) press brakes represent a significant advancement in press brake technology, offering unparalleled precision and automation. These machines are equipped with computer controls that allow for the programming of complex bending sequences, reducing the need for manual intervention. CNC press brakes are particularly beneficial in industries where precision and repeatability are paramount, such as electronics and medical device manufacturing.
The ability to store and recall bending programs enhances efficiency and reduces setup times, making CNC press brakes ideal for both high-volume production and small-batch custom work. Their integration with CAD/CAM systems further streamlines the design-to-production process, ensuring accuracy and consistency in every bend.
Electric Press Brakes
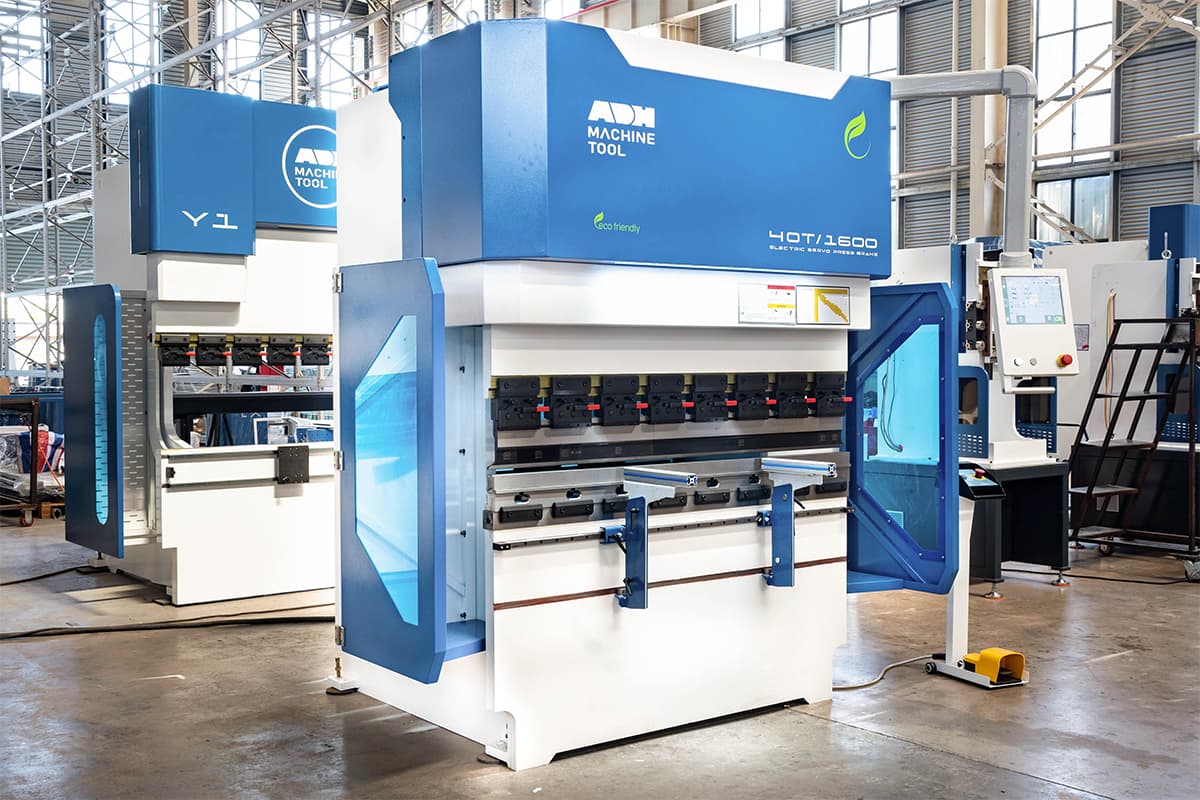
Electric press brakes are the latest innovation in press brake technology, known for their energy efficiency and environmental benefits. Unlike hydraulic systems, electric press brakes use servo motors to drive the bending process, resulting in lower energy consumption and reduced maintenance requirements. These machines offer precise control over the bending speed and force, making them suitable for applications that demand high accuracy and minimal environmental impact.
Electric press brakes are increasingly popular in industries focused on sustainability and cost-effectiveness, such as renewable energy and green building construction. Their quiet operation and reduced energy usage make them an attractive option for modern manufacturing facilities aiming to minimize their carbon footprint.
III. What is a Press Brake Used For
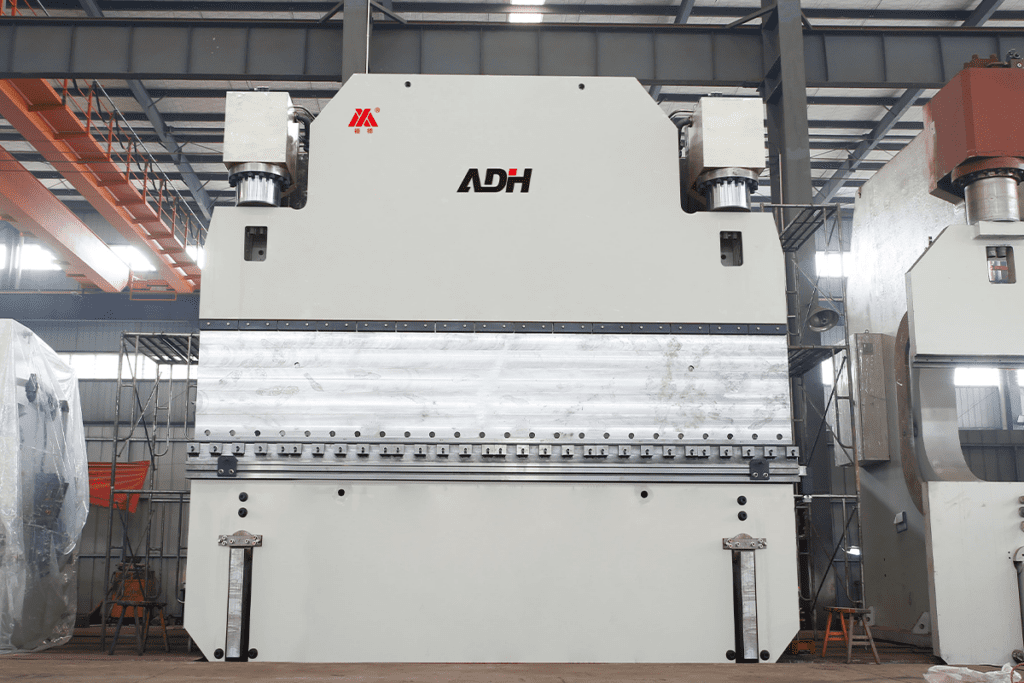
The press brake is a metal fabrication machine for bending and forming metal sheets or sheet materials. This machine utilizes hydraulic or mechanical pressure to exert pressure on the top press brake punch and bottom die, thus transforming the metal angle and shapes. It is a piece of equipment in the metal fabrication industry and its primary use of press brake includes:
Bending Metal Sheets
Metal bending is one of the core applications of press brakes, wherein flat sheets of metal are subjected to mechanical force to produce a variety of angular bends and shapes. The bending process is fundamental in creating components like brackets, enclosures, and panels.
Typically, a punch and die setup is used on a press brake to achieve the desired bend angle and radius. These bends are integral in the manufacturing of parts for automotive bodies, housing for electronic devices, and household appliances. The precision provided by press brakes ensures that each bend meets strict tolerances, resulting in high-quality, consistent products.
In addition to precision, these machine tools provide flexibility in handling various materials and thicknesses. They can accommodate a wide range of metals, including steel, aluminum, and copper, each with unique properties that influence the bending process.
Sheet Metal Forming
Beyond simple bending, press brakes are also pivotal in the comprehensive forming of sheet metal. The sheet metal forming process involves several techniques, each tailored to achieve specific outcomes. Common methods include bending, as well as more specialized processes such as hemming, beading, flanging, and coining.
These techniques allow for the creation of features that enhance the functionality and aesthetics of metal parts. For instance, hemming is used to fold the edge of a sheet for reinforcement or safety, while beading adds rigidity and visual appeal.
Industries that heavily rely on sheet metal forming include HVAC, automotive, aerospace, and consumer electronics. In the HVAC sector, press brakes are used to form ducts, plenums, and other components that require precise dimensions and airflow characteristics.
The automotive industry utilizes sheet metal forming for body panels, chassis parts, and interior components, where both structural integrity and aesthetic appeal are paramount. Aerospace applications demand high precision and lightweight structures, making press brakes indispensable for forming aircraft panels and support structures.
Custom Fabrication
The customization capabilities of press brakes are another significant application, enabling manufacturers to produce bespoke metal parts tailored to specific requirements. From prototyping to batch production, press brakes can execute complex designs with precise bends and shapes that meet unique project specifications.
Modern press brakes, particularly CNC models, offer programmable controls that facilitate rapid adjustments to bending sequences and tooling setups. Custom fabrication often involves making parts for machinery, architecture, and specialty consumer products.
For example, custom metal brackets designed for unique load-bearing applications in construction or bespoke enclosures for specialized electronic equipment are commonly produced using press brakes. The ability to quickly adjust settings and tooling on modern press brakes enhances their versatility and responsiveness to custom fabrication needs.
Safety is a key consideration in custom fabrication, as the complexity of bespoke designs can introduce unique challenges. Press brakes are equipped with advanced safety features, such as programmable safety zones and real-time monitoring systems, to protect operators during intricate bending operations. Proper training and adherence to safety protocols are essential to ensure a safe working environment and prevent accidents.
Production of Structural Components
The production of structural components is a critical application of press brakes, serving as a cornerstone in industries such as construction, infrastructure, and renewable energy. These components, which include beams, frames, and support structures, are essential for ensuring the integrity and stability of buildings, bridges, and other large-scale projects. The precision and reliability of press brakes make them indispensable tools in the fabrication of these vital elements.
Press brakes are particularly suited for producing structural components due to their ability to handle a wide range of materials and thicknesses. This versatility allows manufacturers to work with various metals, including steel, aluminum, and stainless steel, each chosen for specific structural properties. The ability to apply precise force and control during the bending process ensures that each component meets the stringent specifications required for structural applications.
In the construction industry, press brakes are used to fabricate components such as I-beams, channels, and angles, which form the backbone of buildings and infrastructure. These elements must withstand significant loads and environmental stresses, making precision in their production paramount. Press brakes provide the accuracy needed to achieve the exact dimensions and angles required for these components, ensuring they fit seamlessly into the overall structure.
The renewable energy sector also benefits from the capabilities of press brakes in producing structural components. Wind turbine towers, solar panel frames, and other renewable energy structures require robust and precisely formed metal parts to ensure efficiency and durability. Press brakes enable the production of these components with the necessary precision and consistency, supporting the growth of sustainable energy solutions.
In addition to their precision, press brakes offer the flexibility needed to accommodate custom structural designs. This is particularly important in projects where unique architectural or engineering requirements dictate the need for bespoke components. The ability to quickly adjust press brake settings and tooling allows manufacturers to produce custom structural elements efficiently, meeting the specific demands of each project.
Safety is a critical consideration in the production of structural components, given the high forces involved and the potential for large, heavy workpieces. Press brakes are equipped with advanced safety features, such as light curtains and emergency stop functions, to protect operators during the bending process. Proper training and adherence to safety protocols are essential to ensure a safe working environment and prevent accidents.
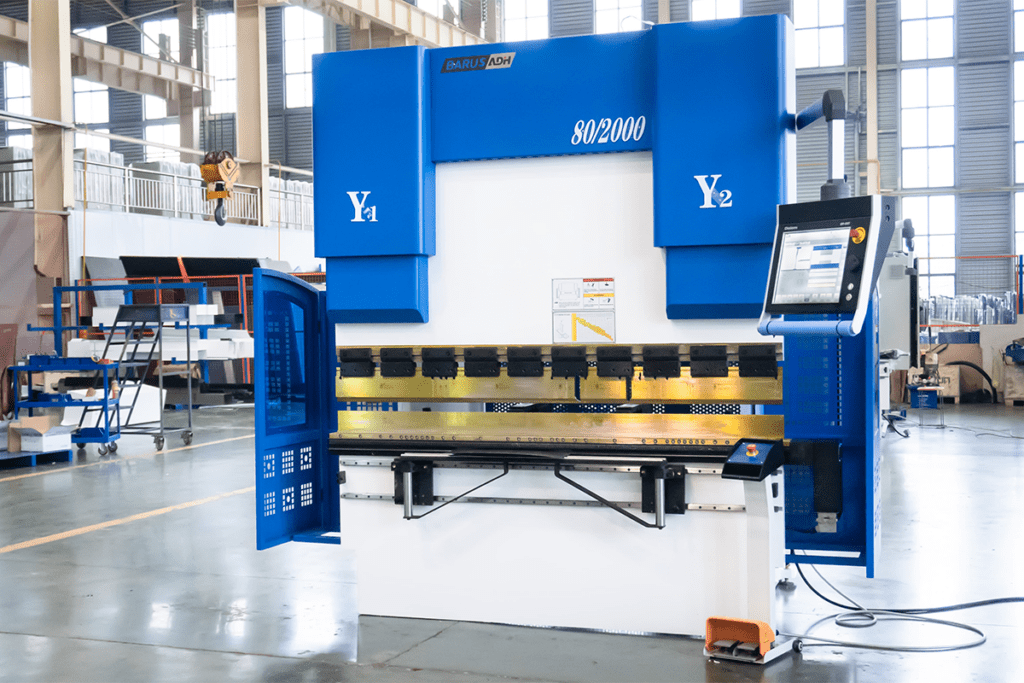
IV. What is a Press Brake Specifically Used For
Workshop and car body area:Â the press brake is widely used in manufacturing car body and workshop components, such as car body components that need bending, like rackets, doors, and roofs, as well as various panels that need to be manufactured via press brake.
Electrical appliances field: TV casings, refrigerator door panels, and metal casings inside and outside various electrical appliances are all bent and formed by thin metal plates using press brakes.
Building structure field:Â roof structures, such as beams, exterior panels, etc., need to be bent and formed using a press brake.
Ventilation duct field: various ventilation ducts that need to be bent in the HVAC system are mostly formed using bending machines.
Auto parts field:Â many parts that require bending, such as automobile exhaust pipes, brackets, and covers, are formed using bending machines.
Household appliances field:Â the inner shell of the oven and various mechanical structures are also formed using a bending machine.
Light machinery field:Â for example, light machinery such as blades also uses bending machines for bending processing.
Prototyping and customization area: the machine is valuable for prototyping and custom manufacturing. They allow manufacturers to create samples, prototypes, and small batches of metal parts with specific bends and shapes according to custom requirements.
Metal furniture and decorative Items field: they are utilized in producing metal furniture, fixtures, and decorative items, which enable the metal sheet to bend and shape to create furniture frames, table legs, brackets, and artistic designs.
Aerospace industry: press brakes are used to fabricate critical components such as engine enclosures, brackets, and parts for wing assembly. The ability to bend high-strength materials accurately is vital for safety and performance in this sector.
Medical equipment: the medical industry relies on press brakes for creating frames for medical devices, surgical tools, and various equipment that require precise metal forming.
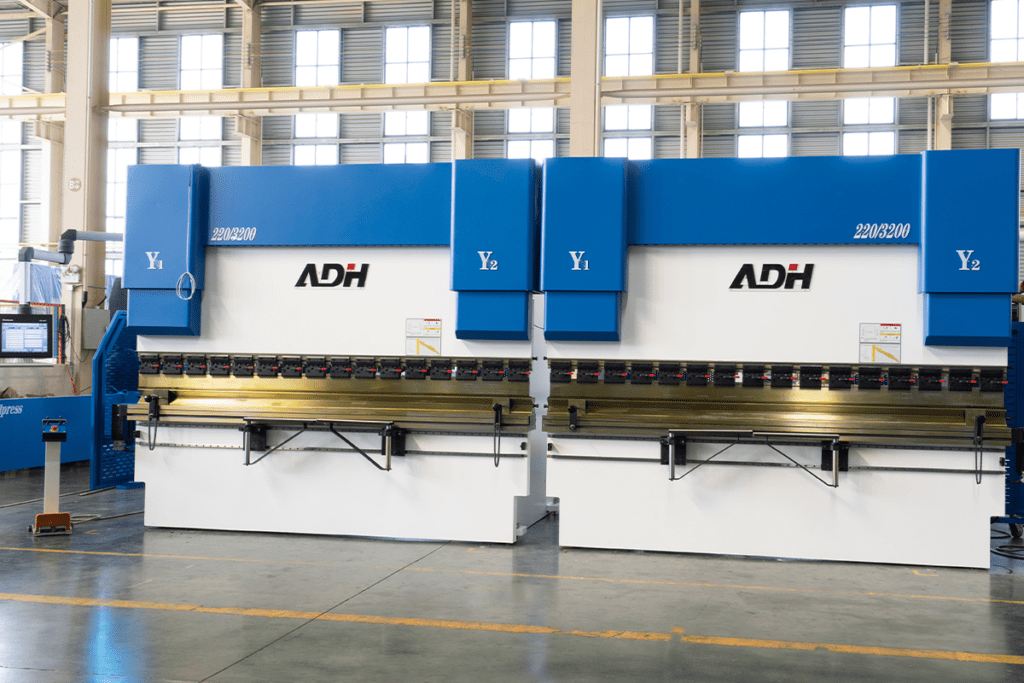
V. FAQs
1. What materials can be processed using a press brake?
Press brakes are versatile machines capable of processing a wide range of materials, including various metals such as steel, aluminum, copper, and stainless steel. Each material has unique properties that influence the bending process, such as malleability, tensile strength, and thickness.
Understanding these characteristics is crucial for selecting the appropriate press brake settings and tooling to achieve optimal results. Additionally, some advanced press brakes can handle non-metal materials like plastics and composites, expanding their application scope.
2. How does a CNC press brake differ from a traditional press brake?
CNC (Computer Numerical Control) press brakes represent a significant advancement over traditional press brakes by integrating computer technology to control the bending process. Unlike manual or mechanical press brakes, CNC models allow for the programming of complex bending sequences, ensuring high precision and repeatability.
This automation reduces the need for manual adjustments, minimizes human error, and speeds up setup times. CNC press brakes are particularly beneficial in industries requiring intricate designs and consistent output, such as aerospace and electronics manufacturing.
3. What are the safety precautions when operating a press brake?
Safety is paramount when operating press brakes due to the high forces involved in the bending process. Operators should be well-trained and adhere to established safety protocols, including the use of personal protective equipment (PPE) such as gloves and safety glasses.
Modern press brakes are equipped with advanced safety features like light curtains, emergency stop functions, and programmable safety zones to protect operators from potential hazards. Regular maintenance and inspection of the machine are also essential to ensure safe and efficient operation.
4. Can press brakes be used for non-metal materials?
While press brakes are primarily designed for metalworking, some models can process non-metal materials such as plastics and composites. The ability to handle these materials depends on the machine's design and the specific properties of the material being processed.
Non-metal materials often require different tooling and settings to achieve the desired bends without causing damage. Manufacturers should consult with press brake suppliers to determine the machine's compatibility with non-metal materials and ensure optimal performance.
5. What is the typical lifespan of a press brake machine?
The lifespan of a press brake machine varies depending on factors such as usage frequency, maintenance practices, and the quality of the machine. Generally, well-maintained press brakes can last several decades, providing reliable service throughout their operational life.
Regular maintenance, including lubrication, inspection of hydraulic systems, and replacement of worn components, is crucial to extending the machine's lifespan and ensuring consistent performance.
6. How do I choose the right press brake for my manufacturing needs?
Selecting the right press brake involves considering several factors, including the type of materials to be processed, the required precision and complexity of bends, production volume, and budget constraints.
Manufacturers should evaluate the specific needs of their operations and consult with press brake suppliers to identify machines that align with their requirements. Additionally, considering future growth and technological advancements can help ensure the chosen press brake remains relevant and efficient over time.
7. How does a press brake improve production efficiency?
A press brake improves production efficiency through several strategies and technological advancements. Retrofitting existing machines with modern features like CNC controls automates many aspects of the bending and forming processes, reducing manual intervention and minimizing human error. These upgrades can add programmable features, allowing for more complex bend sequences and increased productivity.
Effective tool management is also crucial. Proper marking, storage, and quick loading/unloading systems significantly reduce setup times. Automated systems like tooling carousels and robot arms can quickly and accurately position tools, streamlining the production process.
Modern press brakes equipped with CNC systems can store complex programs and bend sequences, enabling quick setup and consistent results across multiple runs. Offline programming software allows operators to create and simulate bending programs away from the machine, saving valuable machine time and minimizing downtime. CNC controls provide greater precision and reduce cycle times, leading to more efficient operations.
Optimizing the workflow around the press brake enhances efficiency. A well-organized workspace layout minimizes movement and reduces task completion time. Implementing lean manufacturing principles, such as just-in-time production, reduces waste and optimizes processes. Automated material handling systems, like robotic arms or conveyor systems, transport materials to and from the press brake, reducing manual handling and speeding up production.
Developing standard operating procedures (SOPs) ensures consistency and efficiency across operations. Regularly reviewing and analyzing processes to identify areas for improvement helps refine workflows. Collecting data on cycle times, scrap rates, and other performance metrics can identify bottlenecks and inefficiencies, leading to continuous improvement.
Automation features such as material handling robotics or sheet followers assist operators in handling heavier parts, ensuring consistent results and increasing productivity. Press brakes offer versatility in handling various materials and thicknesses, making them a flexible tool for different applications. With the right tooling, a press brake can bend materials from thin gauge steel to thick plate steel accurately and efficiently.
By implementing these strategies, fabricators can significantly enhance the efficiency of their press brake operations, leading to higher productivity, reduced material waste, and improved overall production quality.

Download the Infographic With High Resolution
Green Pet Tape,Pet Adhesive Tape,Polyester Adhesive Tape,Insulation Masking Tape
Kunshan An De Qing Electric Technology Co., Ltd. , https://www.andeqing.com